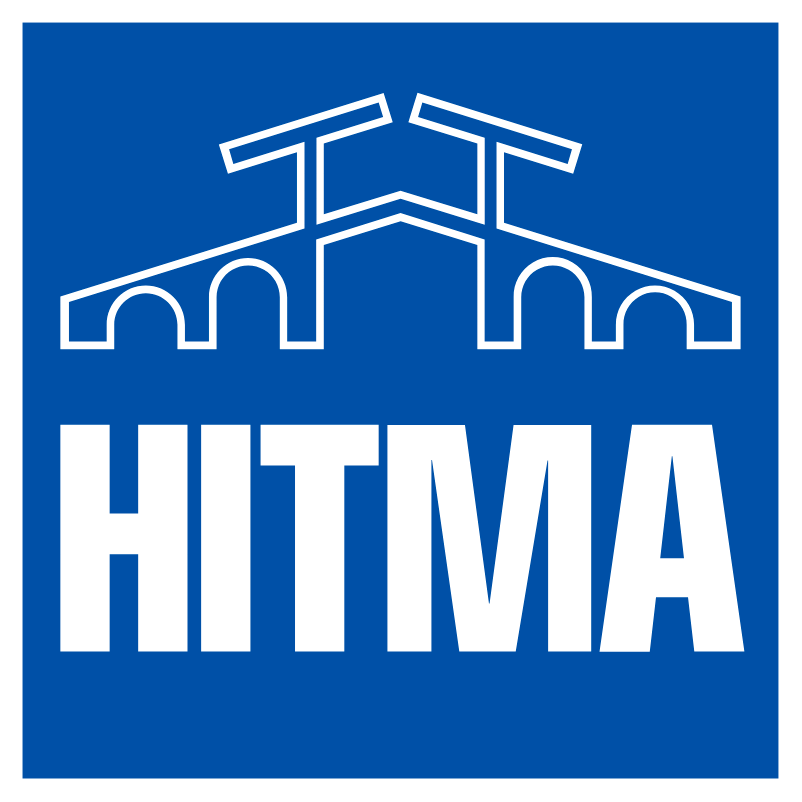
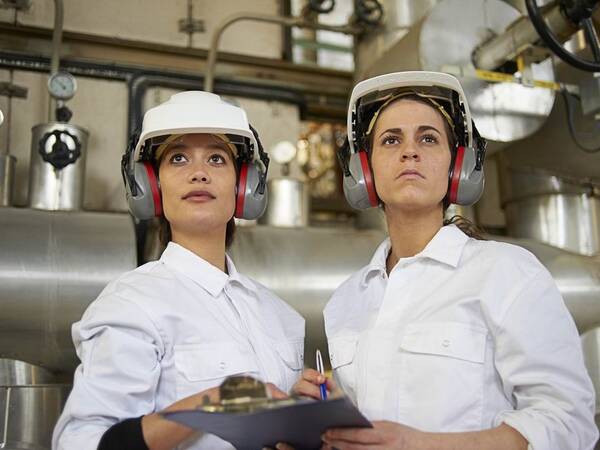
In my role as a specialist in pressure protection, I am involved in projects across various sectors, including the chemical industry. My role involves advising industrial companies and engineering firms on spring-loaded safety valves for overpressure protection. When selecting, purchasing, and installing safety valves, it is not only about ensuring optimal safety for people, the environment, and surroundings, but also about minimizing product loss and saving energy. After all, overpressure leads to energy and product loss, which costs money.
Safe Pressure Relief
The PC 50 pneumatic actuation, applied to the safety valves of IMI Bopp & Reuther, offers a controlled system for safe pressure relief. This system is especially used when standard spring-loaded safety valves do not meet the strict operating conditions. This is the case, for example, in systems with high operating pressures, increased density requirements, limited opening and reseating parameters, and critical applications, such as superheated steam.
With the help of a PC50 Pneumatic Control unit, processes can operate at higher set-pressures than with spring-loaded safety valves alone.
Moreover, product loss during overpressure situations is minimized because the safety valve re-seats much faster, allowing the process pressure to drop quickly back to a safe level.
One of our customers from the chemical industry chose safety valves with reliable pneumatic support for these reasons.
Inspection at the Manufacturer
IMI Bopp & Reuther always provides a quality check, which is normally also carried out as an incoming inspection at the customer’s site. If desired, this inspection can also be attended ‘live’ at the IMI Bopp & Reuther factory in Germany. The customer I mentioned above chose this option.
The advantage of quality control at IMI Bopp & Reuther's factory is time savings, as the necessary documents and certificates, including the results of the live test, can be inspected on-site and any minor deviations can be corrected immediately.
The inspector from the customer was impressed by IMI Bopp & Reuter's German"grundlichkeit" and High quality.
With the help of a PC50 Pneumatic Control unit, processes can operate at higher pressures than with spring-loaded safety valves alone.
Capabilities and Advantages of the Pneumatic Control Unit
IMI Bopp & Reuther has been supplying the PC 50 pneumatic auxiliary option, also known as the CSPRS Controlled Safety Pressure Relief System, since the late 1980s. Below, I will explain how it is composed and what the capabilities and advantages are.
Standard Safety Valves
A standard safety valve, without pneumatic control, has opening and closing characteristics that depend on the dimensions and the closing force exerted by the spring. If the force generated by the process pressure is greater than the force exerted by the spring, the safety valve opens and the excess pressure is released through the safety relief valve outlet. As soon as the process pressure drops to a set safe value, the spring force closes the valve. During this cycle, product (gas or liquid) is lost.
- In steam applications, you lose pressure/energy, and thus money.
- In chemical applications, such as the production of ethylene, you lose a toxic and explosive product, creating safety risks.
Examples of Standard Safety Valves
Pneumatic Assist PC50/Controlled Safety Pressure Relief Systems
With the PC50, you support the opening and closing cycle of a safety relief valve with an air cylinder mounted on top of the valve (see image). The air pressure supports the force of the process pressure and thereby the closing force of the spring up to the set pressure, which we call the ‘loading air’. The loading air supports the force exerted by the spring, providing a greater closing force. This allows the operating pressure to be closer to the set pressure. The ‘lifting air’ supports the ‘blow down’, so excess pressure can be released more quickly (2-5% of the set pressure). The safety valve closes quickly, reducing product and pressure loss.
Failsafe
In case of a failure in the air pressure supply, the spring in the air cylinder will push the load and lifting pistons apart, reducing the force acting on the piston rod. In this way, the safety valve will still function as a normal safety relief valve without affecting the set pressure.
Assisted Safety Valve
Conclusion
Controlled safety valves are primarily used when standard spring-loaded safety valves cannot meet the strict operating conditions.
Consider:
- High operating pressure (very close to the set pressure, typically >90%)
- Increased sealing requirements
- Limited opening and reseating parameters
- Critical applications
- Requirement for frequent in-service testing of safety valves
Does this apply to your company, and do you have any questions about it? Please feel free to contact me.