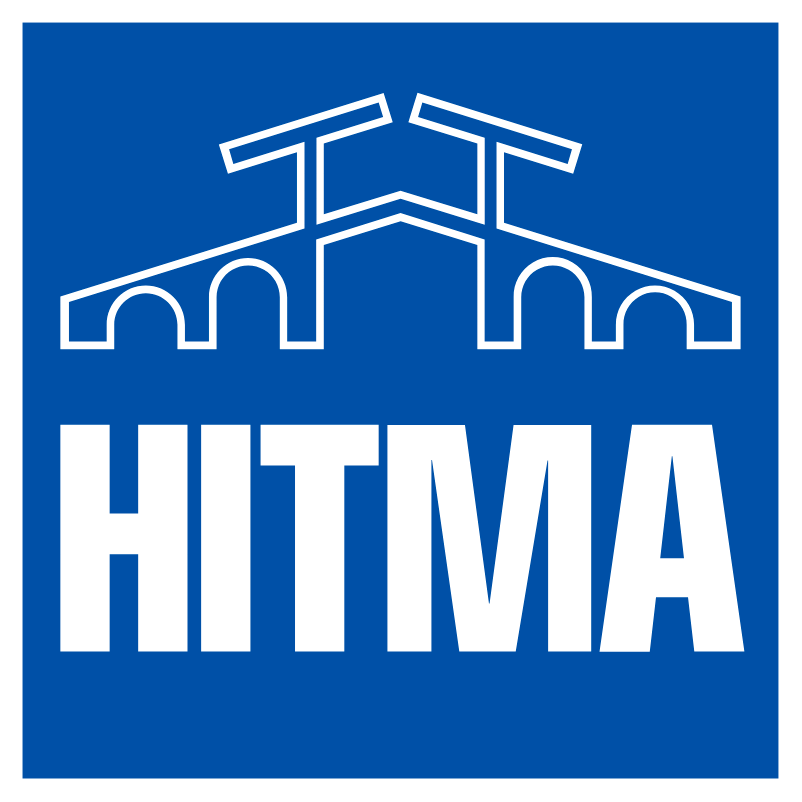
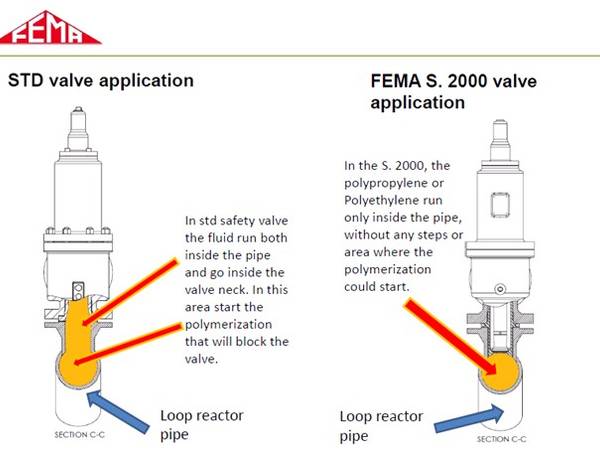
My story goes back to the end of March 2014. It just goes to show how long projects in the valve industry can take. Especially when it comes to special, customised valves for critical applications.
Pumps & Valves
It all started during the Pumps & Valves trade fair (26 & 27 March in Antwerp Expo). During this trade fair for pump installations and equipment for industrial processes, we shared a stand with our ‘sister’ from the Indutrade Benelux holding company, Hanwel Belgium.
Blocked nozzles
At one point, a trade fair visitor stepped onto our stand with a pressing question. This process engineer from a large chemical company is having problems with valves that do not open properly. Due to polymerisation of the medium, the inlet nozzle on the pipeline becomes clogged. Therefore, he is looking for a pressure safety valve without dead ends. This way, he wants to prevent blockages when the liquid in his process polymerises and prevent sticking of the disc and seat when he has to deal with a sticky highly viscous medium.
Custom-made valves
I offer this gentleman something to drink and he comes and sits quietly with us on the stand. Together we discuss the application. I take extensive notes of his story. My thoughts immediately turn to our supplier Fema. This Italian manufacturer of, among other things, spring safety valves for the (petro)chemical, oil and gas and cryogenic industries has specialised in tailor-made solutions for challenging applications. Fema does not do standard valves. Since the beginning of their existence (in 1952 the company started with safety relief valves for loop reactors), their products have been custom-made.
Technical meetings
Some time after the fair, I call the customer. I am curious about the state of affairs. We agree that I will visit him and his colleagues from the Piping department for a technical meeting. During the meeting, it became clear that we can certainly offer this company a solution for this demanding polymer application. I call Fema's specialists and explain the situation. They will figure out how to design the most suitable valve for this application. Later, Fema's technicians come over to the Netherlands to discuss the design with the customer and me.
Lower maintenance costs
The customer is convinced of the possibilities and indicates that I may continue this project with Fema. A long process follows. Fema's engineers start drawing and regularly inform us of the status. After intensive cooperation between Fema's engineers, Hitma Process and the chemical company, the client approves the drawings. The result: the perfect valves for this application. These safety valves follow the contours of the pipe exactly and there are no blind spots (see image below).
Exactly what the customer wants. In addition, the customer also saves on maintenance costs with these valves. Thanks to the sophisticated design, these valves have a longer maintenance and cleaning interval. A pleasant additional advantage.
I am proud of the final result of this extensive project. Together with Fema, I was able to offer this chemical company a suitable solution, which improves the client's process safety and also saves costs.