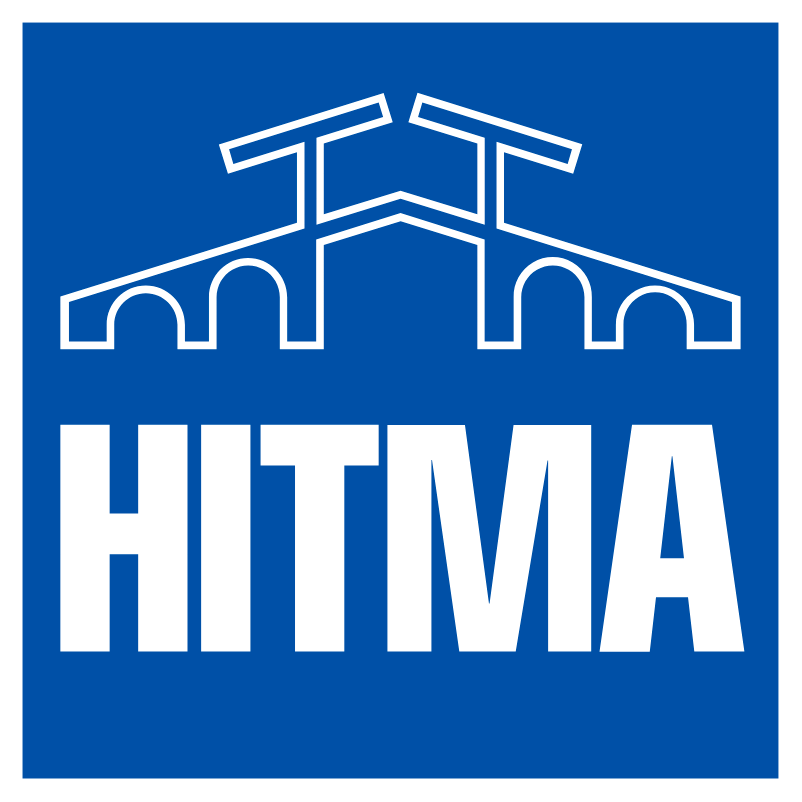
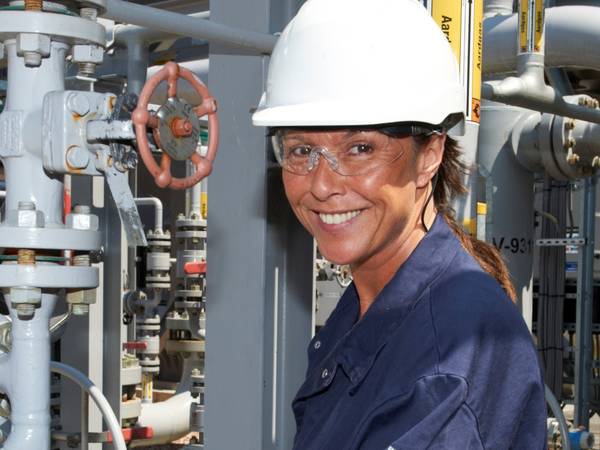
From customers who work with spring fuses in practice, I sometimes get questions about the influence of back pressure on spring fuses. In this blog, I will try to shed more light on this subject. I will do so based on the results of extensive tests with spring protectors of different manufacturers by the University of Milan.
Before I discuss the results of the research, I will first give a brief description of the different types of pressure and commonly used terms. It should be noted that the tests were conducted with a gaseous medium (gas/vapour). For liquids, the outcomes would be different.
Pressures and associated terms in safety valves
Pressure definitions
Back pressure
Back pressure is the pressure on the outlet side of a safety valve (pressure relief device) resulting from the pressure in a discharge system.
Back pressure
We distinguish between three types of back pressure:
Back pressure – superimposed constant
2. Back pressure – superimposed variable
3. Back pressure - built up
Superimposed or built-up back pressure has a strong influence on the opening and flow capacity of safety valves. It is widely recognized that this function is related to a reduction in the disc lift and/or the occurrence of subsonic flow through the valve.
Laboratory tests by the University of Milan
In laboratory tests conducted by the University of Milan on safety valves from five different brands, specially designed to operate under back pressure, a difference was found between the performance guaranteed by the manufacturer and the actual valve performance. This difference can be so significant that the protected equipment exceeds the MAWP (maximum allowable working pressure).
The certified set pressures of the safety valves, when used under atmospheric back pressure conditions, were close, but there was a significant difference when the back pressure was increased from the atmospheric value. This was particularly the case when the back pressure ratio (ratio of absolute back pressure to relief pressure) was increased by 25%. The use of a bellows can help in this regard but does not solve the problem.
Study on valve performance under different conditions
The experience gained by the University of Milan in the laboratory for research, development, and certification of valves led a safety valve manufacturer to test valve behavior in five different applications. The tested valves were ordered with the same technical specifications, including the requirement to operate under back pressure.
|
Results of atmospheric back-pressure tests |
|
||
Valve |
A B |
C |
D |
E |
Blow down % |
37 % 7.3 % |
6.7 % |
5.6 % |
5.33 |
K/Knom At 10% over pressure. Table 2. Summary of atmospheric |
1.02 1.0
back-pressure test results |
0.95 |
1.01 |
0.95 |
Results of atmospheric back-pressure tests
Here are the main results of the tests conducted under atmospheric back pressure conditions for the four safety valves. K is the actual discharge coefficient, while K-nom is provided by the manufacturer under atmospheric back pressure.
The most notable feature is the particularly high blowdown value of valve A. It is almost five times higher than indicated by the manufacturer. The rest of the data is reasonably consistent with the provided values.
Results of tests with built-up back pressure
In Figure 1, you can see the results of the tests conducted on the five valves. The graphs show a reduction in both the manufacturer-specified (dotted line) and the actually measured (solid line) discharge coefficient versus the back pressure ratio.
The K / Knom ratio represents the ratio between the actually measured discharge coefficient at a specific back pressure ratio and the discharge coefficient specified by the manufacturer for the same valve operating under atmospheric back pressure.
The results show that the expected decrease in flow rate for valves B, C, and E is significantly underestimated. Moreover, a very surprising result was found for valve E. This valve shows a dramatic decrease in flow capacity when the back pressure reaches 18%. No further tests were conducted on this device, as the bellows broke when the valve was operated during the first overpressure test.
According to the researchers' report, the bellows functioned correctly when the built-up back pressure test was performed, but this hypothesis cannot be confirmed. However, this incident highlights the importance of the reliability of the bellows and supports the regulation: "In the event of a bellows failure, the safety valve, when opened, will not exceed its certified capacity by more than 1.1 times the maximum allowable pressure (design pressure) of the protected equipment."
For valve A, we see that the capacity reduction trend is anticipated by the manufacturer and that the reduction in flow capacity is relatively low. It should be noted that at a back pressure ratio of 68%, the blowdown coefficient (coefficient of discharge) has only undergone a 20% reduction. On the other hand, the valve has significant problems with reseating. This was also observed in the atmospheric back pressure tests and will also be noted in the supersonic back pressure tests.
The manufacturer of valve B states that the discharge coefficient is not sensitive to back pressure until it reaches 50%, at which a 3% reduction in K is expected. However, contrary to this, the experimental results show that the discharge coefficient follows a progressively linear line, starting at a back pressure ratio of 20% to 48%, where the discharge coefficient is about 2/3 of that of atmospheric pressure. Moreover, the valve shows clear instability at the same built-up back pressure ratio, and the disc tends to close.
The outcomes of these tests underline the need for a well-defined test procedure for evaluating the behavior of safety valves operating under back pressure.
Regarding valve C, the manufacturer claims that the built-up back pressure does not affect capacity. The graph clearly shows that this does not align with the actual lift behavior of the safety valve. The measurements show a dramatic reduction in flow capacity. Even at a back pressure of less than 30% (K / K-nom = 0.63). As the back pressure increases, the discharge coefficient (discharge coefficient) decreases to a minimum value of 43% of the nominal value.
The manufacturer of valve D indicates that no reduction in discharge coefficient is expected for back pressure within 25%, while measurements show a reduction of K / K-nom to 0.95. The flow capacity decreases to 80% of the nominal rate for a back pressure ratio of 34%, after which the safety valve quickly reseats.
Results of superimposed back pressure tests
Tests under 'superimposed back pressure' are aimed at verifying the functional and flow capacity characteristics of safety valves within an overpressure limit of 10%, evaluated based on the set pressure measured in atmospheric back pressure tests.
Valve A was tested at three different back pressure values up to a back pressure ratio of 65%. All tests show the same characteristics. The valve pops before the overpressure of 10% is reached, and the discharge coefficient reaches the same value measured in the built-up back pressure tests for the same back pressure ratio.
As mentioned earlier, this clearly predicted behavior is followed by a fairly high blowdown. In particular, the blowdown decreases compared to the atmospheric tests (37% in tab. 1) and continues to decrease with increasing back pressure: rising from a back pressure ratio of 40% to 65%, the blowdown decreases from 16.5% to 12%, still above the manufacturer's specified limit of 7%.
Valve B pops up before the overpressure of 10% is reached, but only at a back pressure of less than 33%. For higher back pressure, a pop-up occurs at an overpressure rising to 13% at 37% back pressure, corresponding to the limit indicated in the technical specification. Once the valve is open, the discharge coefficient reaches the same values as measured in the built-up back pressure tests. Naturally, the flow capacity is very low when the safety valve does not open. The blowdown remains within the indicated limits.
Valve C opens within the 10% overpressure and closes within the indicated limit. The discharge coefficient always reaches the same values as measured in the built-up back pressure tests. However, the flow rates are very small compared to the specified values (see valve C in fig. 1).
Valve D opens within 10% overpressure only for a back pressure of less than 25%, as specified by the manufacturer.
Above 25%, the valve requires an overpressure of 16% to open for a back pressure of 30%. The blowdown is as specified by the manufacturer, and the discharge coefficient matches the value recorded in the built-up back pressure tests.
Conclusions of the study
What can we conclude from the results of these operational and flow tests conducted on five commercial safety valves that were delivered according to the same technical specifications, as discussed and documented? After comparing valve performance with the manufacturer's information, the following observations were made:
- Atmospheric back pressure tests show reasonably good agreement with the manufacturer's statement for four of the five valves, while only one sample shows a blowdown of 37% instead of the indicated 10%.
- Superimposed and built-up pressure tests show multiple deviations from the manufacturer's specified values, both in terms of operation and flow through the valve.
- In one of the five cases, the bellows broke at the beginning of the back pressure tests. This indicates that in practice, when the valve needs to open under back pressure conditions, the process equipment may be exposed to a pressure higher than 1.1 times the maximum allowable pressure. This could be due to the valve's inability to open within the overpressure limit and/or the reduction in flow capacity caused by poor disc lift and/or the occurrence of a subsonic regime, even when the back pressure ratio is lower than the critical level (0.528).
Need for a defined test procedure
The outcomes of these tests underscore the need for a well-defined test procedure for evaluating the behavior of safety valves operating under back pressure. It is challenging to test a complete range that must meet the limits of the test setup. Laboratory tests conducted on safety valve models show that the dimensions and the ratio of the valve body, from the outlet to the nozzle area, strongly influence flow capacity within the same size range.
Therefore, it is only possible to reasonably measure the performance of a full range of safety valves under back pressure through extensive laboratory testing. However, these tests are crucial. They will lead to better pressure equipment and greater safety for end users.